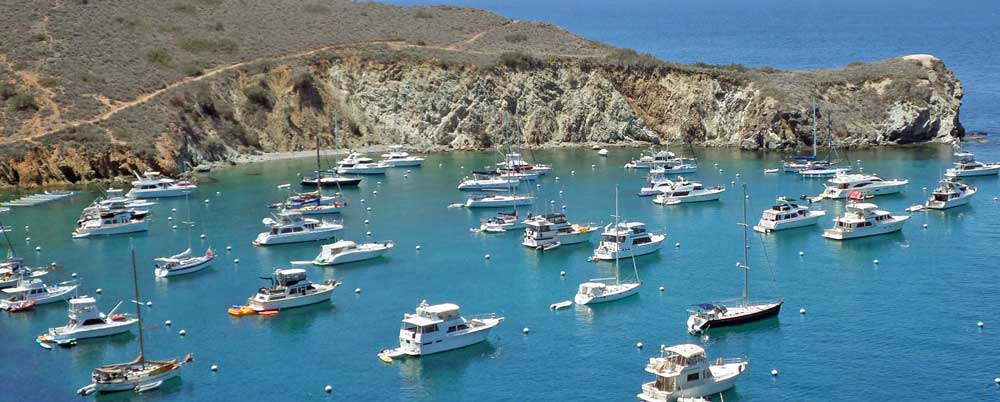
Why Corrosion Resistance Matters in Boat Lights
Boat lights are constantly subject to corrosion from exposure to cleaning agents and saltwater. The latter, also known as aqueous corrosion, is responsible for diminishing light performance. According to a report released by NACE International, an institution that specializes in environmental protection and public safety, corrosion accounts for over $276 billion in losses across the United States (or 3.1 percent of the country’s GDP) per year.
In the marine sector, saltwater is to blame for corrosion on boats, docks and structures near the ocean. The presence of natural salt has a hygroscopic effect on exposed surfaces, which promotes its corrosive qualities. At an atomic level, the electrochemical process breaks down refined surfaces into simpler, more stable forms, which can greatly reduce its protective applications. One of the best ways to prevent corrosive compounds from destroying your boat lights is to invest in corrosion resistant luminaries.
Corrosion Resistant Lighting Designs and Mechanisms
Corrosion resistant boat lights support a robust design that can help reduce the possibility of premature failure when facing unpredictable marine conditions. Lighting manufacturers incorporate corrosion resistant materials, such as brass, stainless steel and glass, during production for added protection. Out of the three, stainless steel is the most common material used for marine fixtures. To promote its resistive features, the metal is treated with thick paint, baked on glazes or special coatings, which also increases its tolerance to high temperatures. Compared to aluminum, stainless steel is better at maintaining the structure of the lamp’s frame by up to 50 percent, and is less likely to warp under extreme environments. Plastics are not ideal for corrosion resistant boat lights because they warp easily when exposed to unstable elements, such as UV light.
Traditionally, glass is used to house the lamp or bulb. Its transparent and sturdy properties are highly favored by operators in the marine sector. It is important to consider that corrosion resistant boat lights should also actively prevent the entry of saltwater. Gaskets and rubber or plastic cord rings may be installed around the luminary’s housing or cord ends to ensure corrosive agents and moisture does not affect the internal components (wirings, ballast or driver- just to name a few) and performance of the unit.
Things to Consider
Lighting approval ratings dictate the capabilities of boat lights when exposed to erratic marine conditions. For example, UL rated boat lights for wet locations are manufactured to deter the accumulation of water in live parts and electrical components that are prone to malfunction in corrosive environments (Wet Locations, from UL Standard Publication 1598). Moreover, International or Ingress Protection (IP) ratings provide information on the boat light’s ability to withstand dust, pressure and temporary immersion. Most consumer boat lights carry IP ratings between IP62 and IP66, while industrial boat lights may hold ratings between IP67 and IP69K- protection from total dust ingress and steam-jet cleaning.
Larson Electronics is a leading industrial lighting manufacturer that specializes in explosion proof luminaries, solar-powered LEDs, portable light towers and power distribution panels. With over 40 years of experience, the Texas-based establishment provides comprehensive solutions for companies with complex lighting requirements. For information about Larson Electronics’ selection of commercial lighting equipment, please check out their website.
Leave A Comment